How do we prove our containers will perform exactly as we say they will, especially when we launch a new or redesigned ULD? We do lots of jigsaw puzzles. Not literally, of course, because that would be weird. But that is how compliance engineer Rolf Plagmeijer describes the extensive ULD testing we do at VRR: finding a way to fit many different pieces together.
ULD testing is a crucial part of the manufacturing process, so we asked Rolf, one of our five compliance engineers, to explain how we test our ULDs. The short answer is thoroughly and enthusiastically. The longer (but more interesting) answer is below. The ULD testing process can be complex, but Rolf keeps it simple for those of us without an engineering degree!
Rolf: why is it essential to test the design of a new or modified ULD?
We have to prove that our designs do what we expect them to do. We can’t just say that a cover is waterproof or fire-resistant, for example. We have to demonstrate to the safety agency (EASA) that our designs comply with strict aviation regulations. If we don’t submit test results and analytical calculations, we can’t get our ULDs certified for airworthiness.
But we also have to demonstrate to our customers that our products meet their exact specifications. Last but not least, we want to prove to ourselves that we’re meeting our own high standards. In other words, testing every aspect of a design justifies the claims we make about our ULDs.
How do you test a ULD design?
There are various ways to test a ULD for structural integrity. One approach is to analyse its strength using a finite element method (FEM). Analysing the strength of our products is particularly useful for completely new designs. The product engineers will come to us in compliance and ask, "Do we need to do a physical test or can you do a finite element analysis (FEA) to check the strength of our design?”
If it’s the latter, we import their model into the simulation program and make some assumptions. Then we run an analysis to determine the strength and potential improvements for the ULD design. This tells us if certain parts are too weak and need reinforcement. It can also tell us where we can reduce the material to reduce the weight. Our analyses are validated by testing and some component-testing may be involved as well.
Another approach is physical testing. We usually do this when an existing ULD is given new features. For instance, we're currently designing a container with a new kind of door. New design aspects always trigger a ULD test cycle because we can't test that by analysis alone; we have to test it physically if we want to get the ULD design approved By EASA.
Want to know more about certification testing? Hear from Certification Manager Matthijs van Barreveld how we guarantee the airworthiness of ULDs!
How long is a typical ULD test cycle?
There's no such thing as a typical test cycle! It depends on the specific test and how complicated it is. Doing the analysis and creating a report can take between two and four weeks, and a physical test might take a day or so, maybe longer if we use an external lab. But it’s the preparation and analysis that takes the most time. It can take a couple of months from start to finish to fully test a new design feature before we can submit our calculations and test results to EASA for certification.
Tell us more about using FEA to analyse the strength of ULDs
All materials have certain properties, including a maximum stress level they can handle. So, when we import the design into our FEM program, we apply loads to the model in different directions according to regulations. The program tells us precisely the stress level that each element of a ULD can handle and then colour-codes the stress points for us.
Take the forward load test on one of our containers as an example. Its structure should survive a load of 100,000 N (22,500 lbs) in the forward direction while the base is restrained in specific conditions for three seconds. We use those requirements as input, and the results show us the design’s stress levels. If the stress is too high in one area, we might suggest adding an extra rivet to lower the stress.
If we're not 100% sure about the analytical outcome—maybe the model does not match reality exactly or we’ve made too many assumptions—we test it physically to see what happens and to validate our model. This is why we always need to test new design features.
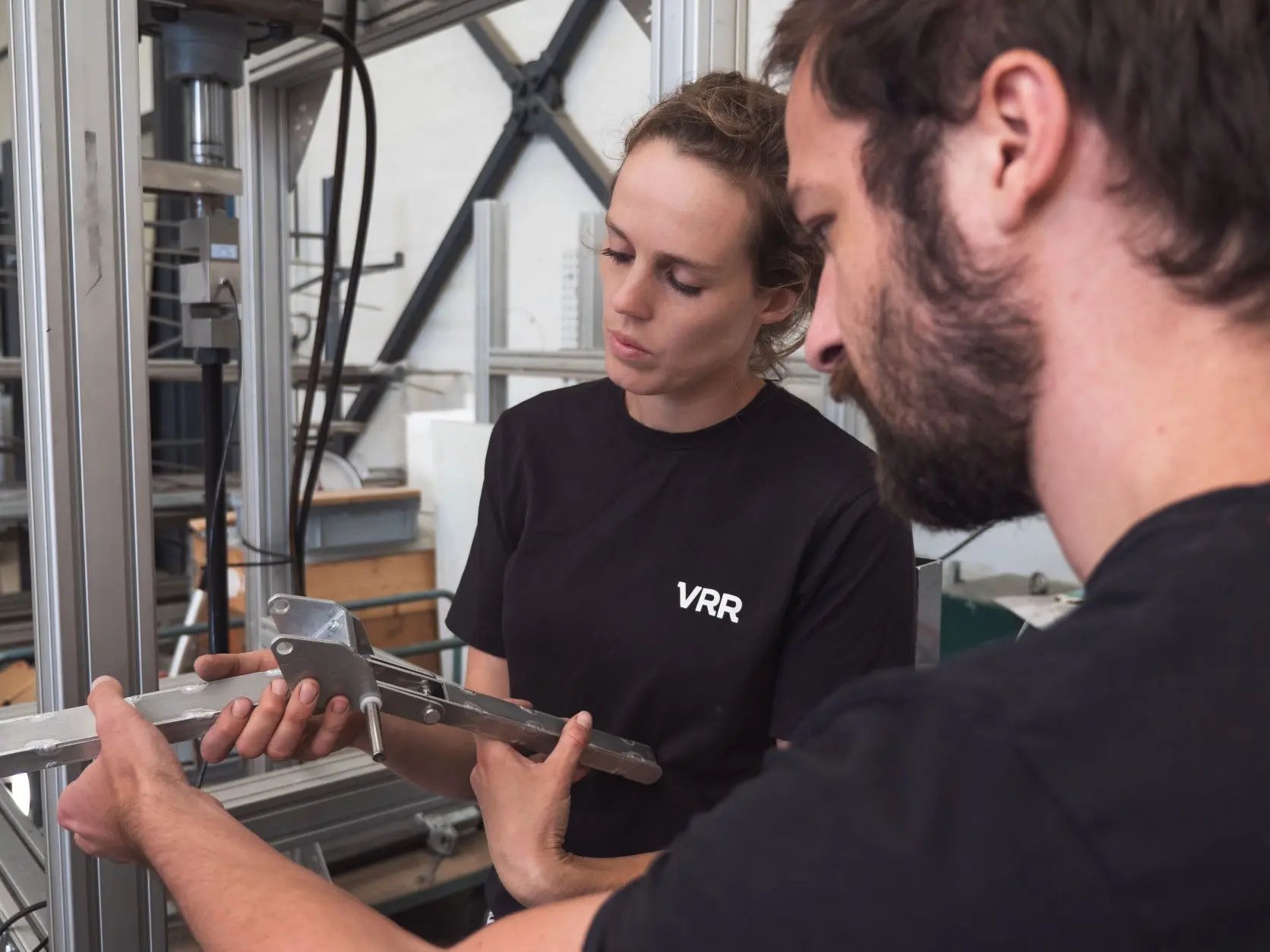
Are there different types of physical testing?
Physical testing can be divided into two categories: design verification tests and official certification tests. The latter ensures compliance with EASA regulations, but design verification tests can be anything, from full-scale tests to testing certain design elements.
For example, we’ve installed new locks on one of our containers, but we weren't sure how strong they were. The supplier couldn't tell us either. So, we did some analysis, and then we came up with a physical test to prove that our calculations matched reality.
Our certification team often devises and performs physical tests for our design engineers. We’ve even set a standard container alight to see how it burns using our fire-resistant containers in a Class A fire test. This can be exciting to watch. But sometimes, if we don't have the necessary equipment or expertise in-house, we’ll use an external lab for things like flammability and UV tests.
How do you physically test a ULD’s strength?
It depends on the type of test. For certification tests, we design and build a custom test frame to accommodate the entire ULD. That actually involves a lot of work and analysis. Then, we place the empty container in the frame, add significant weights to get the desired load and centre of gravity, and remove the support structures to see how the ULD responds.
We’ve even used a crane to hoist a loaded ULD to see what happens. Hopefully nothing, but that would also be boring! But for smaller design details, we test the ULD with our frame in Wieringerwerf or use external test labs.
What challenges do you hit along the way when you're doing a physical test?
The biggest challenge is coming up with a good test plan because you have to try and anticipate what will happen, and some tests are very complex. The other challenge? That nothing usually goes according to plan, especially with tests you’re performing for the very first time. Then you have to be creative and come up with a new plan.
I enjoy doing “first” tests the most. They’re like jigsaws.
You have to look at every piece of the puzzle to come up with a plan. I particularly like it when engineering is involved, as it makes the test more collaborative and exciting. It's always interesting to see if you’ve mitigated all the problems first time around. Usually not!
Finally, Rolf, what makes VRR stand out when it comes to testing ULDs?
As I see it, we’re serious about producing ULDs that comply with the highest industry standards, we’re open to improvements, and we try to stay one step ahead of the market.
We may not have an R&D department on the scale of Boeing or Airbus, but we do have considerable compliance expertise and a network of reputable labs that we collaborate with. Most importantly, if we say something is waterproof or fireproof, we can back up our claims.
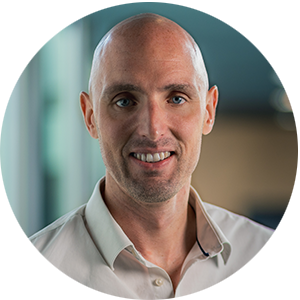