When you order a Unit Load Device, you probably look for the safest and most efficient one possible. After all, you want to protect your cargo and your bottom line. But as the demand for innovative and customised ULDs continues to grow across the air cargo industry, manufacturers are faced with a dilemma: how to push the boundaries of engineering and still comply with strict aviation safety standards.
At VRR, we pride ourselves on our ability to create original and custom products for a wide variety of air transport solutions, so we have to be good at getting ULDs certified (and we are). Certification proves the airworthiness of a ULD. But what does it take to ensure that every single ULD you buy from us meets the rigid requirements of civil aviation authorities?
We speak to Matthijs van Barreveld, Certification Manager at VRR, who explains all. Matthijs joined us in March 2021 when his company IGB—a leading provider of certification support—merged with VRR. His expertise in data-rich and complex engineering and analysis processes gives our customers even faster throughput and greater access to specialist knowledge.
Why are ULDs certified for airworthiness?
It’s pretty simple really. Certified ULDs are designed to be directly restrained by the aircraft’s Cargo Loading System, and it’s that interface that makes them subject to stringent certification standards. If a ULD doesn’t meet these standards, it can’t be placed in the Cargo Loading System.
Some people think a ULD—whether it’s an aircraft pallet and net combination or an aircraft container—is just a way to transport and protect cargo. It’s true that they’re essential to shipping carriers and freight forwarders, but they’re also an essential part of flight safety.
Tell us more about these certification standards
The most common certification standards are the Technical Standards Orders, or TSOs, set by the FAA and EASA. Here at VRR, we deal mainly with EASA because we’re based in Europe, so we normally work to the requirements set out in ETSO C90. These approvals by EASA are accepted by the FAA, though, because there’s a bilateral agreement between the two regulatory authorities.
The ETSO C90 covers all aspects of a standard ULD, from design, testing and production to operations, repair and maintenance. As long as we comply with all the applicable parts, you have an airworthy ULD and not simply a metal box.
What if a ULD isn’t a standard design though?
Good point. At VRR, we’re often asked to change the design of a ULD so that it can carry a certain type of cargo or be loaded onto a specific type of aircraft.
If those changes mean the ULD no longer meets the TSO standard—maybe the base size is different, for example, so it will fit on a certain plane—we have to get a Supplemental Type Certificate or STC.
How does VRR get its products certified?
By being really good at certification, of course! Seriously though, getting ULDs approved for use is essential for an innovative company like ours. That’s why we have a team of six compliance engineers (including me) dedicated to the certification of our ULDs. Some of us studied mechanical engineering, others have degrees in automotive or aviation engineering.
Meeting aviation safety standards isn’t easy. They’re set high for good reason. So manufacturers like VRR must prove conclusively that any ULD can withstand a high load while restrained in an aircraft’s hold and in accordance with the TSOs, not to mention a bunch of other requirements such as fire properties requirements. If we can’t do that, the ULD won’t be certified.
But I should point out that it’s not just the Certification department that’s involved in the certification process. Our colleagues in Sales, R&D, Production and Quality also play a key part.
What does the certification process involve?
Well, we can break it down into six broad steps:
- Determine which requirements apply to the ULD’s design
- Determine how we can achieve compliance with the requirements
- Evaluate the design to ensure that it complies with the requirements
- Ensure the design is not overengineered
- Submit calculations and test results to the regulatory authority
- Receive approval for use from the regulatory authority
And how do you demonstrate that a ULD is compliant?
We can evaluate a ULD’s design physically in a test environment. We did that for our fire-resistant container for example. You should watch the short video we made of it, it’s pretty amazing.
However, most tests we do are based on quantitative analysis. Basically, we perform a ton of analyses based on all kinds of data such as literature, supplier specifications and in-house testing. To do this, we use specialised software, either commercial or what we’ve developed ourselves. The output of all that analysis is lots of complicated tables and diagrams.
These analyses prove that the design can restrain the contents of the loaded ULD under extreme flight conditions. Here’s an example of just one of the many requirements that apply to the AKE container, which is a type of LD3 container:
The upload test on an AKE container requires that the structure can survive a vertical load of 43,600 N in the upwards direction while restrained at just 4 locations at the base for a period of 3 seconds.
I admit that pages of strength and load calculations is probably enough to make anyone’s eyes glaze over. Not us, of course. We’re boring engineers, after all. We love deciphering all that stuff. And at the end of the day, all these tests and calculations help us prove that the design as a whole and its individual components meet aviation safety standards.
So you’re testing the design of a ULD purely on its strength?
Well, we use the term ‘demonstrating’, but it’s true that most of our compliance tests do relate to the strength of a ULD. It has to be strong enough to contain extremely high loads even when lifted and restrained. If it’s not, it can crack or shift in the hold, placing the aircraft in danger during flight. And the last thing you want is objects flying about the hold and changing the plane’s weight distribution. That’s dangerous.
We do run other tests, though. The fire-resistant properties of our fireproof containers, for example, and the rapid decompression hatch properties of our cool containers. For the latter, we have to prove the ULD can equalise its internal pressure if the hold’s pressure suddenly drops. This can happen after a structural failure of the aircraft hull.
You said you also check the ULD is not overengineered. What does that mean?
Well, we don’t just check for safety compliance in the Certification department. We do other stuff too, like making sure a ULD isn’t overbuilt or overcomplicated. That can happen in manufacturing, especially when the safety or performance of a product are critical.
For instance, we look at the weight of the ULD, and we check that it’s easy to manufacture even after modifications. Maybe we discover that it could be lighter but just as robust using different materials. Or maybe we suggest removing an unnecessary feature or making a contour smoother to avoid sharp edges. That sort of thing.
How long does it take to get a ULD certified?
That really depends on the ULD and whether it’s a completely new design or a modification on an existing design. A tweak here and there to the design, such as changing the panel’s material from aluminium to polycarbonate, may take us just a couple of days to run the compliance analyses.
For a standard design that’s more customised, we usually spend about a week analysing, but again, it depends on the complexity of the customisation. A new design, on the other hand, such as the one for our inflatable AKE, can take at least 200 hours of analysis, testing and documenting to make sure it’s structurally sound.
Then there’s the time it takes EASA to assess our calculations and test results and come back with an approval. They usually take three months or so. However, for small changes, VRR has EASA’s authority to process them autonomously, which saves us a lot of time.
We usually know at the start of the process—when we draw up the technical proposal—roughly how long the testing and approval stage will take.
Let’s end with a classic question: what do you like about working here?
I’ve been working with VRR for ten years now, but I joined the company only in March of this year when my own company IGB merged with VRR. So far, the merger is really paying dividends. I’m able to apply my expertise in product certification and quality assurance to develop the Certification department, and I get to work with a diverse team of talented people looking for long-term solutions.
At heart, I’m just an engineer, so I’m never happier than when I’m discovering safe, practical, cost-effective solutions for our customers and the air cargo industry. I can definitely do that here.
Many thanks to Matthijs for sharing his perspective on certifying ULDs and the role that the Certification department has in helping VRR create safe and efficient air cargo solutions for the industry. If you’d like to know more about ULD certification and/or our certification processes, you can drop him a line via the contact form.
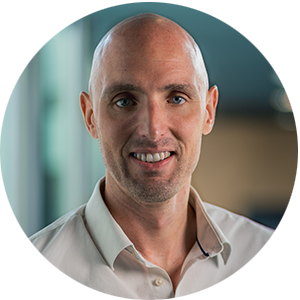