In the early days of the express air freight industry, safety technology was pretty basic. In fact, Unit Load Devices (ULDs), whose primary purpose is to improve flight safety by containing cargo into a standard-sized unit, didn’t even exist for the first ten years of the industry. It wasn’t until 1970 that air cargo containers and pallets made their first flight (on a 747).
The first ULDs were designed for low-volume products. Soon after came containers for livestock. These days, there’s a plethora of ULDs offering express couriers many more market opportunities, from cool containers for the pharma industry to multi-modal solutions for transport integrators.
Of course, in the aviation world, more opportunities mean more safety issues—for the cargo and for the plane. And this has led to numerous challenges and some inventive solutions, especially for ULD manufacturers like VRR. Below we shine a spotlight on five of those safety challenges.
5 safety challenges facing the air freight industry
Safety challenge 1: ULDs are the only aircraft parts that leave the airline’s control and pass through many unregulated hands.
The solution: Get the entire industry to understand how ULDs work and why they are critically important to flight safety.
Most express cargo is transported within ULDs. However, according to IATA, many people in the industry simply do not know that ULDs are actually aircraft parts and that they contribute directly to flight safety. This is a huge problem, especially when you consider that there are over one million ULDs in service around the world and that they are the leading cause of aircraft damage during ground operations.
At the heart of the problem is the fact that most airlines outsource their ULD operations to third parties such as ground service providers, freight forwarders and shippers, although a great option but there’s often zero insight of regulatory authorities. This outsourcing has led to insufficient operator training, inadequate operating environments, and poor ULD management.
To try and rectify this situation, IATA launched a safety campaign in 2016 to raise ULD safety awareness across the industry. The aim of this campaign, which continues to this day, is to ensure that everybody knows how to handle ULDs safely and, therefore, minimise flight safety risks, damage to planes, and damage to the ULD themselves.
IATA estimates that 80% of ULD repair or misplacement costs could be avoided if they were handled and managed correctly. That would save the industry up to a staggering $475 million. We hope that everyone in the industry is learning that a ULD is not just a box.
Safety challenge 2: 5 percent of ULDs with a worldwide total worth of 300million US dollars go missing each year.
The solution: To develop transparent, always-on tracking systems for ULDs.
With around 1 million ULDs being handled by many different parties—some of them unregulated—as they travel around the world, it’s perhaps no surprise that some go astray each year. This is a safety (and financial) problem that everyone in the industry is keen to resolve.
What may surprise you (it certainly surprised us) is the fact that airline-to-airline transfers of containers and pallets are still processed using a paper-based system that IATA set up nearly 50 years ago. What’s more, this ULD Control Receipt doesn’t even cover airline-to-third party ULD transfers. Can technology come to the rescue?
At one time, RFID chips and GPS systems were thought to be the answer. However, they have proved to be unviable from an economic perspective. Fortunately, the introduction of Bluetooth technology has enabled tracking to enter a new and improved phase.
Major freight carriers and ULD management companies have started using Bluetooth-enabled ULD tracking technology to analyse ULD movements. The Bluetooth tags can be linked to the air waybill and the ULD’s serial number, enabling transporters to know where their shipments are at all times.
The ability to track shipments is quickly becoming standard across the industry. Tech providers like Shippo, EasyShip and uShip now offer to connect carriers to tracking systems using ADIs and EDIs (Application Program Interfaces and Electronic Data Interchanges). Meanwhile, the largest global cargo carriers have developed their own tracking systems.
The air cargo industry is also venturing into blockchain territory in an effort to improve transparency. Blockchain is basically a digital ledger of transactions that allows multiple parties to view and audit data but not change it, making it ideal for long supply chains.
It’s still early days, but companies like SITA and AirAsia are convinced that blockchain can enable the ‘always-on’ tracking of ULDs and, at the same time, eliminate inefficient paper systems and manual processes. We’re watching this development with great interest.
Safety challenge 3: Transporting dangerous air cargo safely.
The solution: Complying with worldwide safety standards and developing fire-resistant ULDs.
Dangerous goods are defined by the International Civil Aviation Organisation (ICAO) as articles or substances which, when transported by air, can pose a risk to health, safety, property or the environment. Some goods are obviously dangerous, like flammable liquids and compressed gases. Others are less obviously dangerous, like aerosols, lithium batteries, matches and cigarette lighters.
Safety challenge 4: The threat to aircraft due to incorrect cargo loading and unloading.
The solution: Ensuring industry-wide safety procedures are followed.
These days, there’s a lot of pressure on ground handling personnel to minimise turnaround time (the time during which the aircraft remains parked at the gate). After all, everyone is in a hurry. Express carriers work to tight schedules, passengers and airlines hate delays, and airports want as many flights to take place as possible.
Loading cargo onto an aircraft is not a simple job, however, even with the help of ULDs, which are designed to make loading and offloading easier and quicker. Get it wrong and you risk unbalancing the aircraft. That can result in the aircraft’s nose or tail tipping, the aircraft veering off or overrunning the runway during take-off, damage to the aircraft’s hold during flight, and even loss of control during flight.
Aircraft ground stability is a major safety concern, so cargo has to be loaded with the aircraft’s centre of gravity in mind. Accordingly, IATA’s Safety Audit for Ground Operations (ISAGO) manual requires all ground handlers to implement a Safety Management System that is equal to those implemented by aircraft and airport operators.
Loading and offloading cargo in a certain order is an example of a standard operating procedure covered in the 350+ page manual. It recommends offloading aft holds before forward holds and loading forward holds before aft holds. It also advises a tail-support stanchion or nose tether for certain aircraft types during loading and offloading.
ISAGO, currently the only global programme that is aligned with ICAO Doc 10121, Manual on Ground Handling, is widely seen as helping support a positive safety culture across aviation.
Safety challenge 5: Protecting cargo and the aircraft’s systems and structure from damage
The solution: Designing ULDs that minimise or prevent all risks of damage.
One of the key features of ULDs is their ability to protect cargo from contamination, water damage, infestation and extreme temperatures. They also enable intelligent weight distribution within the plane’s hold and prevent damage to the plane and products, so they are an essential element in air freight safety.
Unfortunately, ULDs are exposed to many shifting conditions as they move throughout the entire cargo chain. They’re moved on dollies, lifted by forklifts, stacked in holds, and exposed to all kinds of weather while waiting to be loaded on a plane or stored in an outdoor airport facility. So, they have to be built to withstand the rigours of air transportation.
It can take months, even years of research to develop a ULD. Countless factors constrain its design and engineering: material durability, account base dimensions, contours and rigidity, maximum weight, and aircraft centre of gravity offset limits. Consequently, all ULDs must comply with a long list of safety protocols and requirements. These include the aircraft’s Weight and Balance Manual, IATA’s ULD Regulations, and the certification standards of the FAA and EASA.
VRR’s new AAX container is a great example of how leading ULD manufacturers continue to invest in research to improve air freight safety standards. The latest version of this main deck container is made from just one piece of aluminium, unlike the current version, which is made out of multiple pieces of aluminium. This clever design has many advantages.
First, there are no sharp components on the inside. All internal parts are flush with the frame and walls, providing a safer environment for cargo. Second, the container has a unique curved profile. This rounder, smoother contour not only fits the aircraft’s hold better (maximising space) but also protects it better because there are no sharp edges to damage the hold’s lining. Finally, it’s weatherproof and can be transported from the tundra to the desert without external weather conditions adversely affecting the cargo.
The air freight industry continues to improve the safety of both cargo and aircraft using a mix of advanced technology, improved processes and global standards. The same goes for the manufacture of ULDs, and we wouldn’t dare call ourselves innovative if we weren’t dedicated to making our ULDs as safe as possible.
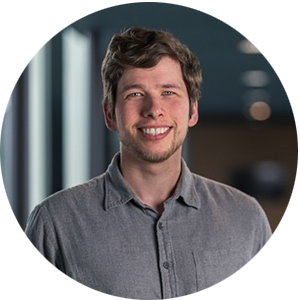