While the world is holding its breath for scientists to develop a vaccine against COVID-19, the air cargo industry is beavering away in the background to ensure the vaccine can be distributed as soon as it rolls off production lines.
Of course, distributing vaccines around the world is nothing new. We’ve been doing it for decades. But what is new is the exceptional scale and timing of the SARS-CoV-2 vaccine programme.
What’s more, it’s come at a time when the air cargo industry is stretched as thin as rice paper, thanks to national lockdowns, restricted air travel corridors, and severely reduced passenger flights (which in normal times carry around 50% of air cargo).
Get ready to distribute billions of vaccines doses
Vaccine manufacturers are already gearing themselves up for staggering levels of production, despite the fact that they’re still conducting trials. They’ve announced a cumulative production capacity of around one billion doses by the end of 2020 and nine billion doses by the end of 2021. In the US alone, they’re preparing to distribute 300 million doses of vaccine next year.
The anticipated vaccination of large swathes of the global population more or less simultaneously is going to take a whole lot of planning and collaboration between pharmaceutical companies, health providers, local and national governments, and—last but not least—pharmaceutical logistics providers, including the air cargo industry.
A long list of logistical questions for the air cargo industry
The air cargo industry plays a crucial role in the COVID-19 vaccine pipeline. Leaving aside the issue of how vaccine distribution is to be prioritised (which will vary per country), there’s a long list of logistical challenges which cannot be fully addressed until it gets answers to questions like these:
• When and where will the first batches of vaccine be ready for distribution? Will there be more than one type of vaccine used to immunise people against COVID-19? More than 170 candidate vaccines are being tracked by the World Health Organisation, nine of which are in large-scale, phase 3 efficacy trials.
• How is the vaccine going to be packaged and transported from the place of manufacture to local distribution centres? What filling and packing materials will be required?
• Will the vaccine come in single-dose or multi-dose vials or manufacturer-filled syringes, and what is the shelf life? Will repeat doses be needed year after year?
• Will there be enough air cargo capacity and flexibility due to the reduction in passenger flights? It’s been estimated that a single Boeing 777 freighter can carry 1 million individual doses of a vaccine. If we follow that logic, we’ll need several thousand freighter planes dedicated to delivering the vaccine.
• Will the limited number of airports around the world that are certified to handle pharmaceuticals be ready for such a huge movement of pharmaceuticals? You can’t fly vaccines into any airport. They have to belong to IATA’s network of certified pharmaceutical trade lanes to ensure consistent standards are met and product integrity is safeguarded.
• What temperature is required to transport and store the vaccine safely? For example, DNA-based vaccines can usually be transported at normal room temperature, while RNA-based vaccines require cold chain or cryo-shipping. On the other hand, frozen vaccines must be stored in temperatures between -50°C and -15°C, while all other routine vaccines can be stored at refrigerator temperatures 2°C and 8°C.
So, with all these questions still unanswered, what can the air cargo industry do to prepare?
Learning from past immunisation programmes
To a certain extent the industry can learn from the past. The transportation, storage and distribution of large amounts of vaccine is bound to be done in phases. Priority for immunisation will probably be given to high-risk groups (e.g. the elderly and those with comorbidities) and certain occupational groups (e.g. public health personnel and law enforcement). The tiered approach to manufacturing and distributing the vaccine should help spread out delivery schedules somewhat, although speed will still be a critical factor.
The likelihood of more than one successful vaccine
It may also be safe for the industry to assume that there will be more than one type of vaccine available and that the wait won’t be too long. The Director of the National Institute of Allergy and Infectious Diseases in the USA, Dr Fauci, said “It is likely that multiple COVID-19 vaccine regimens will be required to meet the global need.”
Reinforcing this viewpoint, the USA’s Centers for Disease Control and Prevention has recently issued guidance to all 50 states, instructing them to prepare to distribute two unidentified vaccines as soon as late October or early November. Whether one or more vaccines will be ready so quickly or, as many others think, in early to mid-2021, it still doesn’t give the air cargo industry that much time to get organised.
Is the air cargo industry ready to play its part?
Distribution of the vaccine is almost certainly going to involve the cold supply chain, so the issue of temperature control will be crucial. If the cold chain lacks the capability to distribute and store the vaccines at the correct temperature, it can’t guarantee their efficacy. Reduced potency would lead to inadequate immune responses and a troubling loss of confidence among patients and providers.
That doesn’t bear thinking about.
But is the air cargo industry ready to handle the shipment of a COVID-19 vaccine to billions of people? Some fear not. After all, the largest vaccination programme in human history is going to take place when the air cargo industry is going through possibly its worst ever crisis.
What’s more, as Neel Jones Shah, Global Head of freight forwarder Flexport has rightly pointed out, “Vaccine supply chains are exponentially more complex than PPE supply chains. You can’t ruin PPE by leaving it on the tarmac for a couple of days. You will destroy vaccines.
Temperature Cold Supply Chain
Unfolding vaccine scenarios: Fridge and/or freezer
To get prepared, the air cargo industry will need to assess all its partnerships, processes and equipment to ensure it can adapt to different scenarios. This is especially true when it comes to the cold chain.
Although we don’t yet know the required shipping and storage temperature for any of the expected vaccines, many health officials are predicting that at least some of them will need an environment of between 2°C to 8°C.
First, not all the vaccines currently being tested are RNA-based (they’re the ones that need arctic-like storage conditions). Second, some pharmaceutical companies are trying hard to develop vaccines that require less stringent standards for refrigeration. This is partly to enable vaccine roll-outs in more remote or underdeveloped areas and partly to encourage continuing investment from external stakeholders.
However, some of the most likely vaccine candidates at the time of writing, including the BN1162b2 and BNT162b2 from BioNTech and Pfizer, would require ultra-low temperature freezers and thermal shipper storage to keep them at a -70°C.
Preparations for distribution and storage are already underway
Signs of preparation for either or both temperature scenarios can already be spotted. UPS, for example, has built freezer farms near its hubs in Louisville, Kentucky, and in the Netherlands to store the most fragile vaccines. Each farm can house 600 advanced freezers, which can each hold 48,000 vials of vaccine at temperatures as low as -80°C.
Meanwhile, demand for dry ice is increasing significantly. Dry ice, which is basically frozen carbon dioxide, is often used to transport temperature-sensitive cargo such as vaccines. The extra demand is starting to create a shortage, so it’s hoped this won’t impede the development of a coronavirus vaccine or stall preparations for the air cargo industry.
Stocking up on cool containers
One positive step that freight forwarders and airline operators can take right now is to ensure they have enough cool containers in their ULD fleets to ship those vaccines that do not require freezing. These temperature-controlled air cargo containers, which come in a variety of shapes and sizes, help airlines, airports and carriers abide by IATA’s strict Temperature Control Regulations.
Cool containers are either passive or active. The passive variety, as the name suggests, don’t actively control the temperature, but they do prevent fluctuations in temperature using a source of cold such as wet ice, gel packs, dry ice or liquid nitrogen.
The active variety monitor and control temperature levels automatically with a system of sensors, ventilators, air ducts, a control unit and a data log. The data log measures the actual temperature inside the container throughout the entire journey, helping to guarantee an unbroken cold chain.
Confidence in our industry partners
The air cargo industry is facing a huge task. Getting ready to distribute these much anticipated vaccines at any time, let alone during a crisis, is no walk in the park.
However, at VRR, we have confidence in our industry partners, who have shown extraordinary resilience and ingenuity in the last few months. And we sincerely hope that our range of certified cool containers will play a small (but important) part in that mammoth distribution.
Find out more about our temperature-controlled containers by contacting one of our specialists at info@vrr.aero.
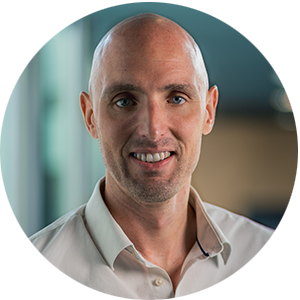